In many ways, waffle weave is a delightfully straightforward weave structure. It is well-suited to four-shaft weaving, and uses a simple point twill threading. It gets its name from the simple fact that it looks like waffles--the cloth is made up of a grid of squares with high walls and deep centers, just like the little divots on a waffle that hold your syrup until you’re ready to eat. Each square is called a cell. The fascinating side of waffle weave is how those cells are created.
The center of each cell is a small dot of plain weave. Above and below that pick of plain weave, there are picks with small weft floats. Move one more pick away from the center in either direction, and there are even larger floats. The same pattern of increasingly large floats is also happening in the warp at the same time. Go one warp end to either side of that center point and there are small warp floats, then larger ones. These warp floats join the weft floats to create little squares, one inside of another. The largest square, made of the longest floats, makes the highest point of the wall of the cell.This is also the border between one cell and the next. The more shafts you’re using, the more layers you can add to these nesting sets of squares. That makes your cells even deeper and your cloth more three-dimensional.
And wow, is waffle weave ever three-dimensional! It might not look that way at first, though. As you weave, you’ll see the little cells building up, but they will be laying flat on the loom. Even after cutting off, you may be dismayed to see that your cloth looks as flat as a simple twill. But don’t despair! Waffle weave transforms enormously in wet finishing. As the fibre blooms or fulls and the cloth pulls together, the cells will deepen. Your flat grid of cloth will become a cushy, thick waffle.
That process of gaining depth through wet finishing really changes the dimensions of your cloth. Waffle weave has much higher shrinkage than other weave structures. Be sure to account for this when designing your own waffle projects. The Waffle Weave Towels that Bryce Wicks designed for Gather, for example, start with a warp that is 20 inches wide in the reed. If you were weaving 2/2 twill on a 20-inch wide warp, you might lose an inch to draw-in and another inch to shrinkage, leaving you with 18-inch wide finished cloth. But the waffle weave towels that start at 20 inches in the reed and at 15 inches after wet finishing! A full 25% is lost from the starting width.
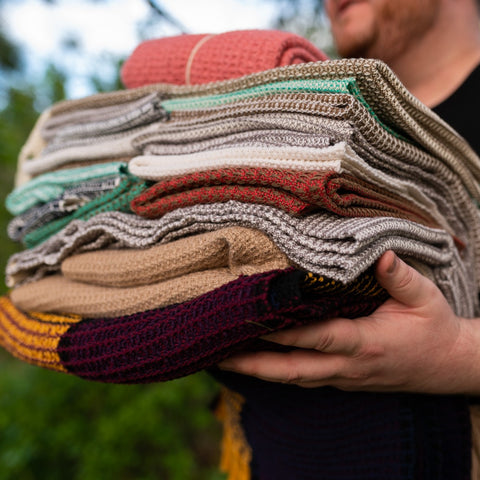
That shrinkage is part of what gives waffle weave one of its best features: its absorbency. As the cells develop, they pull the weaving together into hills and valleys, bending threads up and down across the width and length of the cloth. This means that there’s a whole lot more surface area on waffle weave than there is on flatter cloth. Those threads pulled together into that cell are all available to absorb water. We’ve run trials on waffle weave in the studio where we poured a glass of water straight onto a waffle weave towel and straight onto twill. The difference is dramatic. The cells in the waffle weave hold the water, and the threads that make up the walls of those cells drink it up before it has a chance to go anywhere. For dish towels, hand towels, even bath towels, waffle weave is a dream.
Of course, body and texture are also welcome features on cloth that’s not meant to drink up spills. Waffle weave blankets and scarves are comfortable and cushiony. If you combine a tight sett with the shrinkage typical to waffle weave, you end up with a dense, warm, soothing blanket. With scarves, you might choose to wet finish a bit more gently. This lets the cells develop enough to create some texture, but leaves the cloth with more drape.
If you’re looking for a new challenge waffle weave is well worth a try, if only for the sheer fun of watching it transform in wet finishing. It is like nothing else you will weave!